THG-250 Top Drive Wet Type Rapid Mixer Granulator Top Drive RMG/HSM
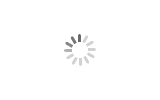
- Wonsen
- China
- 120 days
- Strong
Equipment applications and advantages:
1. Replaces traditional wet granulation.
2.Used as an integrated machine for mixing granulation, solvent recovery, drying and dry cone mill,Airtight level up to OEB5.
3.Product advantages:
Top drive
No water and material can penetration, no black dot or stuck state
Multifunctional all-in-one
can be used as an integrated machine for mixing granulation, solvent recovery, drying and dry cone mill, less material turnover frequency, reduce cross-contamination, low loss, can be selected according to the product process
Mixing uniformity well
Mixing uniformity deviation RSD≤3.5%
Equipment Overview
Equipment Overview
THG Top drive wet type rapid mixer granulator type series owning traditional wet type granulating function. Jacket heating and drying. Both wet type and dry type cone mill.Equipped with advanced PAT online detection technology and automatic control system.It can be used instead of traditional wet granulation, and can also be used as an integrated machine for mixing granulation, condensation solvent recovery, vacuum drying and cone mill, which is especially suitable for highly confined anti-tumor solids, organic solvent solids, new drug R&D and chemical industry.
Top drive wet type rapid mixer granulator is mainly composed of frame, granulating pot, mixing system, granulation system, dry cone mill system, slurry spraying system, vacuum drying system, online detection system, control system, etc.
Control solutions
Control solutions
a. Adopt Siemens PLC and Siemens HMI to ensure the safety, reliability and stability of the control system;
b. Reserved Ethernet interface, convenient for customers to connect SCADA system or information system and extend third-party communication;
c. Use shielded cables, isolators, and reliable grounding to ensure the anti-interference capability of the equipment and guarantee the data stability of the equipment;
d. Use of safety devices to guarantee the safety of the equipment;
e. Use of UPS to ensure data retention in case of power failure;
f.Support outline drawing interactive control to meet equipment cleaning needs;
Working principle
The powder material is conveyed to the granulating vessel by vacuum feeding system or gravity, firstly, the top impeller is rotated and pushed to do fluidization movement to get full mixing, and then the binder is injected through the gun system to make the dry powder material become wet and soft material , which is made into granule under the double action of impeller and high-speed shearing of the granulating chopper,after the granulation is completed, the vacuum system will pump the pot body into negative pressure, while the high temperature medium is passed into the jacket of the pot body, the impeller rotates at low speed to accelerate the evaporation of moisture in the material, and clean compressed air is passed from the bottom of the pot body intermittently during the drying process to bring out the evaporated moisture from the material and accelerate the drying, after the drying is completed, the low temperature medium is passed into the jacket of the pot body to cool the material, and the discharge valve is opened, and the material enters the whole granulator, so that the uneven size of the granules can be made into uniform granules that meet the requirements
Parameters